As the automotive industry accelerates its shift toward electrification, the driveline components that once served internal combustion engines are facing new performance demands. The Universal Joint with Pressed Bearings, long appreciated for its lightweight design and high rotational efficiency, is now being re-evaluated under the lens of electric vehicle (EV) engineering. Unlike traditional combustion setups, EVs deliver instant torque with less vibration dampening from the engine, creating a different stress profile on drivetrain components. This has major implications for how universal joints are designed, tested, and manufactured.
One of the most noticeable differences lies in torque delivery. Electric motors generate maximum torque from zero RPM, which means that the universal joint is subjected to sudden, high-load conditions right from startup. A Universal Joint with Pressed Bearings must be optimized not just for rotational precision but for increased torque capacity without increasing weight. This pushes material selection and surface treatment requirements to a higher level, particularly in areas where space and weight-saving are already design constraints.
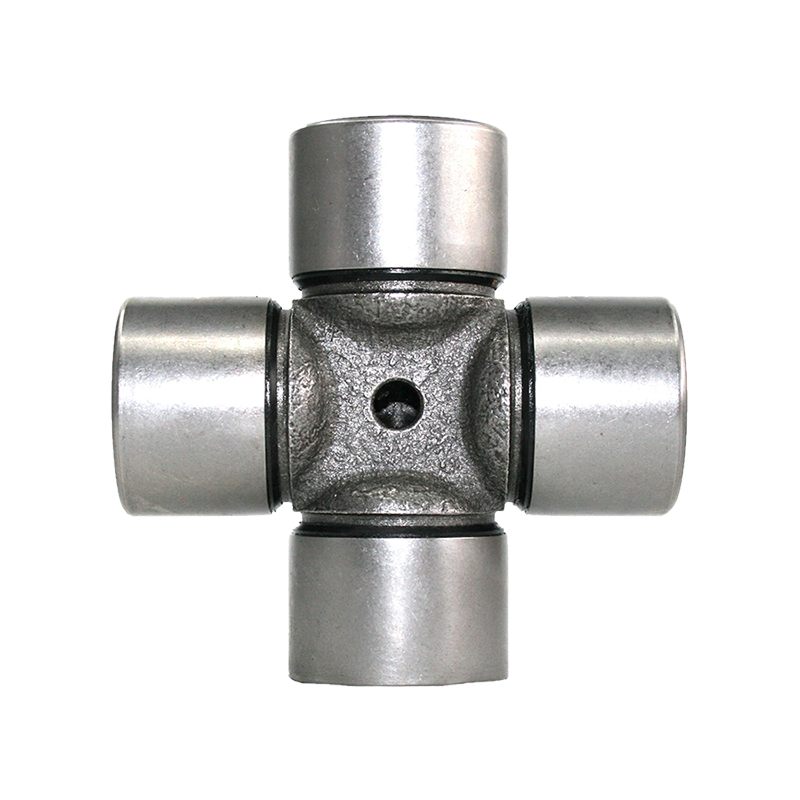
In EV architectures, noise, vibration, and harshness—often shortened to NVH—also become more apparent due to the absence of engine noise. Any minor imbalance or misalignment in the driveline can be clearly heard in the cabin, making the precision and fit of universal joints even more critical. Pressed bearing types, known for their compact design, are often preferred in high-end EV platforms where reducing vibration through balanced rotation is essential. However, achieving that smoothness demands not only tighter manufacturing tolerances but also more rigorous end-of-line testing to catch imperfections early.
Thermal management is another area that’s evolving. While EVs may have fewer heat-generating components overall, driveline parts like the universal joint still experience localized frictional heating, especially under continuous torque. The Universal Joint with Pressed Bearings must be capable of withstanding temperature fluctuations without compromising lubrication or dimensional stability. Lubricants used in these joints must resist thinning under high-speed rotation while still providing long-term protection—especially since many EVs are sealed systems with extended service intervals.
Furthermore, space efficiency plays a vital role in EV chassis design. The push for compact platforms means that every millimeter counts, and components must be integrated more tightly than ever. This has made the smaller profile of pressed bearing universal joints especially attractive. Their reduced size and weight make them easier to fit into limited drivetrain corridors while still maintaining the required angular motion range. As a result, these joints are increasingly found not only in passenger EVs but also in electric delivery vehicles, buses, and even performance-oriented electric platforms.
From a manufacturing standpoint, the shift to electric drivetrains has prompted a wave of new product development cycles. Custom configurations of the Universal Joint with Pressed Bearings are now requested more frequently, with OEMs asking for tailored specifications that meet their unique torque curves, mounting geometry, and lifecycle targets. For suppliers, this means more prototyping, shorter lead times, and enhanced collaboration with customer design teams. The ability to adapt quickly and support low-to-medium volume production runs has become a key differentiator.
Customers exploring EV platforms may not always realize how much drivetrain requirements have changed, but at the supplier level, it’s become clear that the “standard” universal joint no longer fits all applications. We’ve had to modify everything from spline design to bearing preload to ensure our joints perform reliably in electric applications. For forward-looking OEMs and tier-one suppliers, sourcing a Universal Joint with Pressed Bearings that’s already adapted to electric torque and vibration profiles can prevent costly redesigns and improve long-term product performance.
With EV adoption continuing to grow, we see the pressed bearing universal joint becoming a cornerstone of future driveline systems. Our commitment as a manufacturer is not only to meet these new demands, but to anticipate them—offering precision-engineered solutions that match the evolving standards of the electrified era. Whether you’re designing for today’s electric powertrains or preparing for the next generation, making the right joint selection early can ensure better durability, quieter operation, and a smoother ride.
Contact Us