When it comes to the driveline systems of U.S. heavy-duty trucks, universal joints play a critical role in transferring torque efficiently while allowing for angular misalignment. Among the various configurations available, the universal joint with welding plate bearings stands out for specific applications—especially in North American trucks using models like the 5-280X and 5-279X. However, understanding how this type compares to other u-joint locking systems, such as inside lock or strap-type joints, is essential for making the right selection in real-world conditions.
The welding plate variant of the universal joint features bearing caps that are secured externally, typically via welding plates integrated with the yoke. This outside lock design ensures a robust mechanical hold that minimizes movement under load, which is especially advantageous in high-vibration environments. In contrast, inside lock configurations rely on internal snap rings within the yoke ears, which can be more susceptible to displacement when subjected to shock or uneven torque loads. While both designs are used across the industry, welding plate bearings offer added durability where consistent performance is non-negotiable.
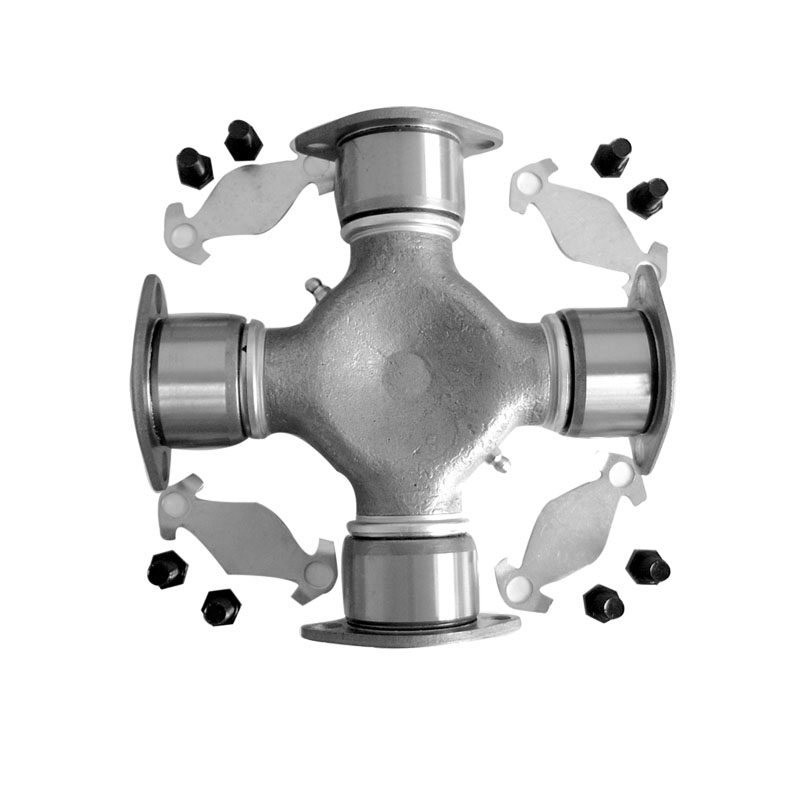
From a maintenance standpoint, universal joints with welding plate bearings can offer greater service life under the same working conditions due to their sturdier locking mechanism. This is particularly relevant for long-haul or off-road trucks that frequently encounter terrain-induced drivetrain stress. Additionally, bearing retention strength tends to be higher in welding plate designs, reducing the chance of cap walk or axial play over time. These small details can make a significant difference in overall reliability and maintenance schedules.
When comparing to strap-type joints, which use bolted straps to hold bearing caps in place, the advantages of welding plate joints become clearer in terms of installation security and vibration resistance. Strap-type joints are generally easier to install and service, making them suitable for light-duty or less-demanding applications. But for fleets prioritizing long-term uptime and lower failure rates, especially in demanding hauling or commercial use cases, welding plate designs are a safer investment.
One common misconception is that all welding plate variant of the universal joint are interchangeable, but even among U.S.-standardized parts, subtle design differences can have a big impact on performance. Universal joints with welding plate bearings are engineered with a different load-bearing philosophy compared to their strap or inside-lock counterparts. Their application in models like the 5-280X is not random—it reflects a response to specific mechanical challenges that traditional joints may not address as effectively.
For OEMs and fleet maintenance managers, making the right choice isn’t just about fitting the part—it’s about optimizing for performance, reliability, and serviceability over time. That’s where professional-grade u-joints with welding plate bearing configurations show their value. As a manufacturer deeply rooted in drivetrain solutions, we emphasize designs that balance strength, durability, and installation efficiency, tailored to the demanding conditions of the American trucking industry.
In today’s competitive aftermarket landscape, choosing the correct universal joint type can directly affect both equipment lifespan and operational costs. Whether you're retrofitting an existing driveline or specifying parts for new assemblies, understanding the differences between these joint styles—especially the advantages of universal joints with welding plate bearings—can lead to better-informed decisions and fewer unplanned downtimes.
Contact Us