Upgrading a truck's driveline isn't just about replacing worn-out parts—it's often a strategic move to improve durability, reduce maintenance downtime, and adapt to changing performance demands. One component where this is particularly relevant is the universal joint. For many fleet operators and truck owners, switching to a universal joint with welding plate bearings can bring measurable benefits, especially when vehicles operate under heavier loads or more aggressive driving conditions than originally intended.
Universal joints with welding plate bearings are commonly found in American heavy-duty trucks, with standard models like 5-280X and 5-279X being widely recognized. These joints feature an outside lock design that offers excellent axial strength and ease of alignment, making them ideal for retrofitting purposes. While stock u-joints in older or mid-tier vehicles might rely on simpler retention methods, upgrading to a welding plate type provides a more secure, vibration-resistant connection—particularly valuable when vehicles are upfitted for specialized uses such as towing, off-road travel, or long-haul freight.
Many mechanics and maintenance professionals recommend this upgrade during major driveline overhauls or engine swaps, when drivetrain geometry might shift slightly. A welding plate bearing configuration can compensate for minor misalignments more effectively, reducing long-term wear on yokes and seals. This is not just a mechanical convenience—it translates to reduced repair frequency and longer service intervals, two things every fleet manager appreciates when calculating total cost of ownership over time.
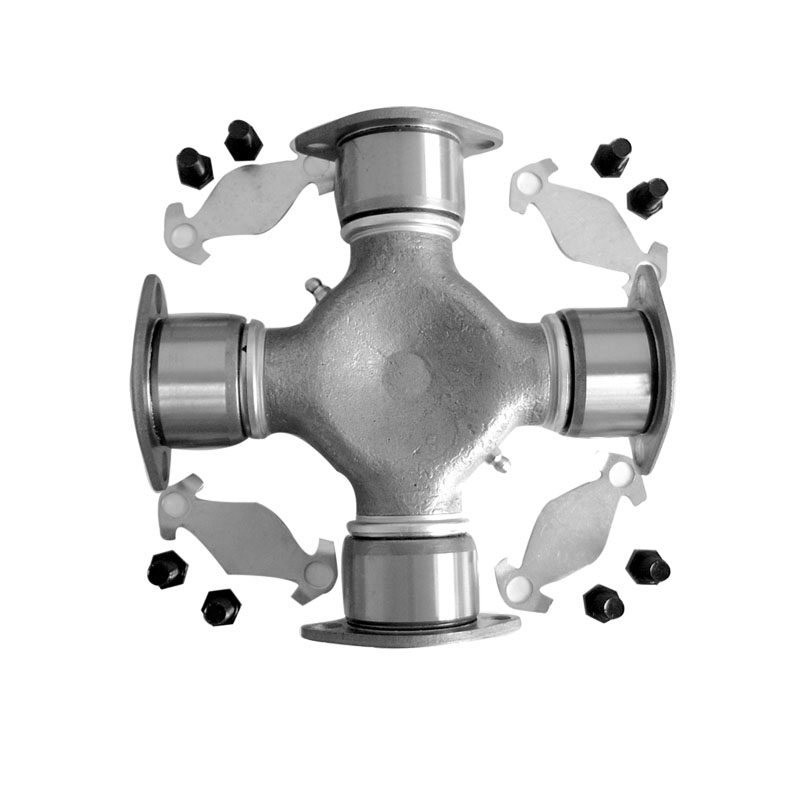
Another factor driving the shift to these joints is material fatigue in older driveline parts. Over time, traditional u-joints may develop micro-cracks or become overly loose due to insufficient load-bearing surface. A universal joint with a welding plate-style bearing cap typically distributes forces more evenly across the joint, reducing the likelihood of sudden failure. This design also allows for easier grease retention and sealing, extending the life of the part even under tough environmental conditions like road salt, mud, or gravel exposure.
The installation process for a Universal joints with welding plate bearings is relatively straightforward for experienced technicians, but it does require proper alignment and torque calibration. It's worth investing in OEM-quality or precision aftermarket units, as improperly machined components can compromise the advantages of the design. Manufacturers like us prioritize tight tolerances and high-grade materials to ensure that every joint can handle the high torque loads modern trucks demand—especially those that see constant use in industrial or commercial settings.
One of the most common questions from prospective buyers is whether these joints are worth the extra cost. While the initial price may be slightly higher than standard u-joints, the long-term savings on labor, replacement parts, and unexpected downtime often make it a smart investment. For fleets that can’t afford unpredictable failures, upgrading to universal joints with welding plate bearings is less of a luxury and more of a proactive reliability strategy.
Ultimately, if you're planning to extend the working life of your vehicles, improve load-handling performance, or simply standardize maintenance with a more robust solution, switching to these specialized u-joints is a move backed by both engineering logic and field experience. As a manufacturer committed to durability and precision, we see this upgrade as a practical enhancement, not just an optional extra.
Contact Us