Manufacturing a Universal Joint with Pressed Bearings involves more than just materials and machining—it’s an exercise in engineering precision and consistency. At first glance, the component may seem straightforward, but when weight optimization, rotational efficiency, and fatigue resistance are required, the real complexity emerges. Pressed bearing versions of universal joints demand especially tight tolerances in their manufacture, largely because their slim, lightweight design leaves little margin for dimensional error. Any deviation in the cup diameter or trunnion alignment can lead to accelerated wear, vibration, or even catastrophic failure under load.
One of the most significant challenges lies in achieving concentricity between the trunnion and bearing cup. In a typical universal joint, minor misalignments can often be absorbed or adjusted during assembly. However, in a Universal Joint with Pressed Bearings, the pressed-fit design offers no such forgiveness. The manufacturing process must therefore guarantee near-perfect symmetry and roundness—often within microns—through advanced CNC machining and in-line inspection. For customers operating in premium driveline applications, such as performance vehicles or high-end industrial equipment, this level of precision directly correlates with product reliability and service life.
Another critical area is surface treatment and hardness consistency. Since the bearing cup walls are thinner by design, surface durability becomes vital. These components often undergo specialized heat treatment processes like induction hardening to strengthen only the load-bearing surfaces without affecting the inner geometry. Achieving a uniform case depth across complex contours, especially when dealing with lightweight alloys, requires a sophisticated understanding of thermal behavior and metallurgical response. A slight inconsistency in hardness can lead to pitting or cracking when exposed to torsional stress cycles.
Tool wear and control of machining environments further complicate things. Because the tolerances are so tight, even subtle changes in cutting tool sharpness, coolant temperature, or ambient shop conditions can introduce variations. Manufacturers must deploy automated feedback systems to monitor these variables in real-time, ensuring that every Universal Joint with Pressed Bearings that comes off the line meets exact specifications. In our own experience, the cost of rework or rejection rises exponentially in high-precision joint production, making preventive process control essential.
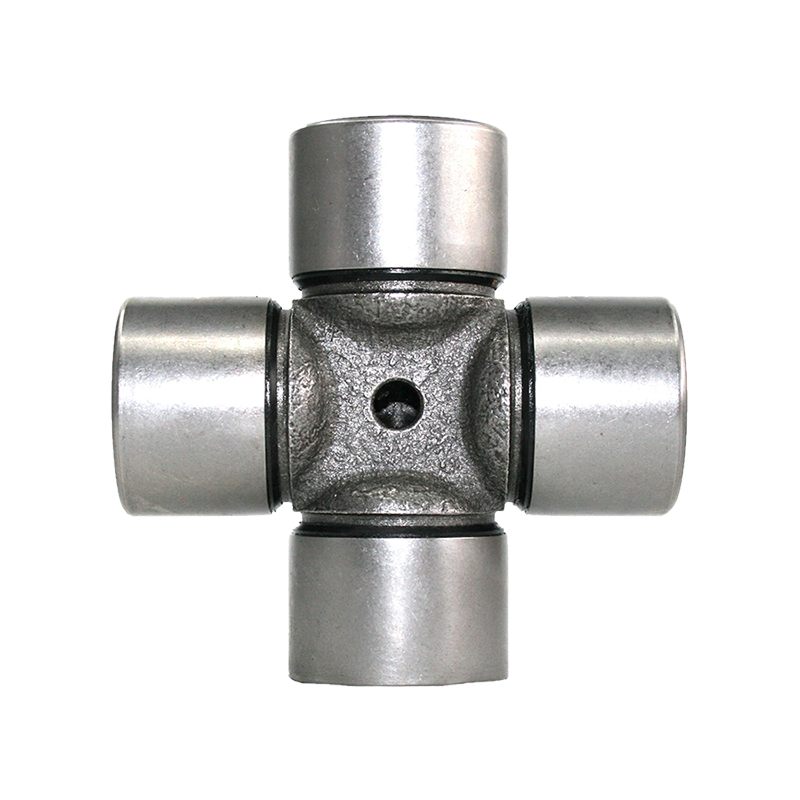
Assembly also presents its own set of challenges. The bearing press-in operation must be executed with just the right force—not too little to risk a loose fit, and not too much to deform the cup or alter the internal geometry. Specialized press-fit fixtures, along with real-time force monitoring, help achieve this balance. For this reason, manufacturers who understand both the mechanical and material science aspects of universal joints are best positioned to deliver consistent quality, especially when working with advanced or proprietary materials.
Inspection and quality assurance are equally demanding. Traditional inspection methods like manual gauges or simple visual checks are insufficient at this level. Coordinate Measuring Machines (CMM), laser scanning, and digital bore measurement tools are now standard in verifying dimensional accuracy and detecting micro-deviations. Each batch of Universal Joint with Pressed Bearings is subjected to these tests before packaging, ensuring our customers receive components that meet or exceed OEM replacement standards, such as those of INA or SKF.
From a production standpoint, these challenges mean higher upfront investment in equipment, training, and process development. But the payoff is clear—consistent, high-performance components that function smoothly at high RPMs and under significant loads. For procurement professionals and engineers alike, partnering with a manufacturer who understands these challenges isn't just a technical consideration; it's a smart business move. Better precision means fewer failures, lower lifecycle costs, and a better end-user experience.
As one of the experienced manufacturers in this space, we've worked hard to refine every stage of our production process for universal joints. When it comes to the pressed bearing version, success lies in the details. And while we won’t claim perfection, we will confidently say that delivering precision at scale is something we’ve come to master. For clients who demand consistent performance from their driveline components, a well-made Universal Joint with Pressed Bearings can make all the difference.
Contact Us