In the world of driveline engineering, weight reduction is more than just a buzzword—it’s a design imperative. But reducing mass in key components like universal joints must be done without compromising strength, precision, or durability. This is where the universal joint with pressed bearings offers a compelling solution. By adopting advanced materials and refined manufacturing techniques, these joints achieve a thinner, lighter bearing cup while still outperforming many traditional counterparts in demanding applications. The end result is a smarter component, not a weaker one.
Historically, universal joints were designed with substantial mass to ensure stability under rotational stress and heavy torque. While that worked for decades, the rise of high-performance and energy-efficient vehicles has shifted design priorities. Every gram counts, especially in rotating assemblies. A universal joint with pressed bearing technology allows engineers to shave weight without sacrificing structural integrity. This is made possible by using specially treated alloy materials that exhibit higher yield strength and fatigue resistance compared to standard steels.
The shape and wall thickness of the bearing cup play a pivotal role here. Pressed bearing designs enable a thinner cup structure without loss of rigidity, owing to uniform stress distribution and controlled deformation under load. In fact, compared to bulkier forged versions, these pressed-bearing U-joints demonstrate more consistent torque transmission and improved dynamic balance at higher rotational speeds. These performance characteristics make them especially suitable for premium driveline systems, where both weight savings and reliability are essential.
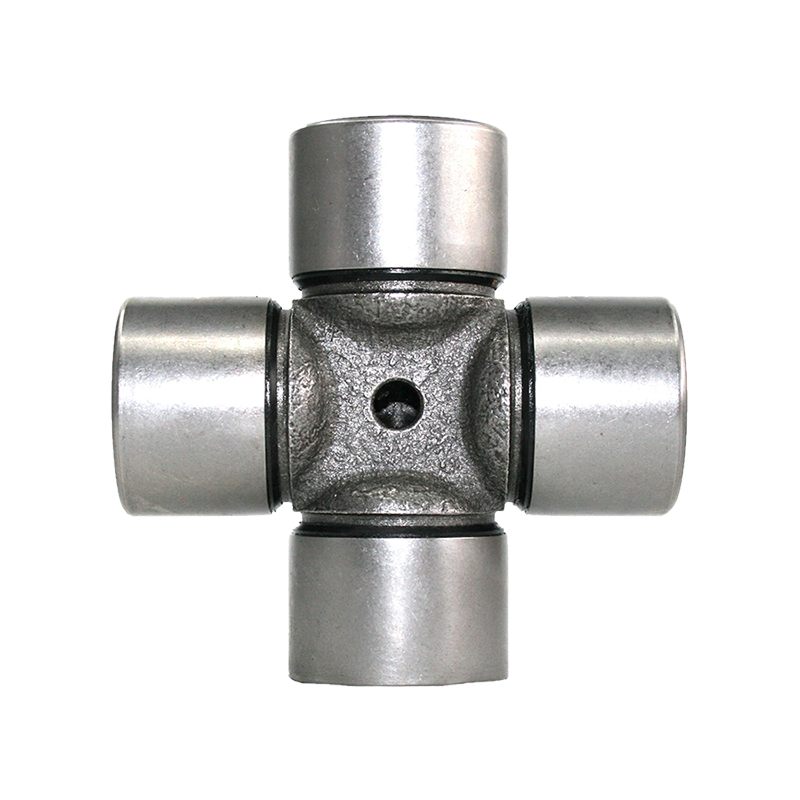
Of course, there are trade-offs to consider. While lighter components reduce overall vehicle weight and rotating mass—contributing to better fuel efficiency and acceleration—designers must account for factors like heat dissipation and wear behavior. Fortunately, the pressed bearing approach meets these challenges with precision engineering. Surface treatments, exact tolerance control, and optimized bearing geometry ensure smooth operation and long service life, even under continuous stress cycles. That’s why major OEMs often opt for these joints in high-end applications.
Moreover, a universal joint with pressed bearings isn't just about performance; it’s about efficient manufacturing and smarter logistics. The lighter weight means lower shipping costs and easier handling in assembly lines. For suppliers and manufacturers, this translates to a leaner production flow and higher throughput. And from a buyer’s standpoint, it means getting a high-value component that fits modern engineering standards without inflating costs. The fact that these joints can seamlessly replace INA or SKF models only reinforces their market versatility.
In real-world usage, feedback from OEMs and aftermarket installers confirms that pressed bearing U-joints are not only meeting performance expectations—they’re exceeding them. From sports utility vehicles to light trucks and performance cars, the shift toward lighter driveline components is proving beneficial across the board. As end-users demand more responsive, fuel-efficient vehicles, components like these play an invisible but crucial role in delivering that experience. When engineered correctly, less material doesn’t mean less reliability—it means more efficiency.
At the end of the day, choosing the right universal joint with pressed bearings is about more than specs; it’s about aligning your driveline system with forward-thinking design. If you're looking to upgrade or specify components that meet today's performance benchmarks without compromising on quality, this is a product line worth exploring. As a manufacturer with industry insight and a commitment to innovation, we stand behind these joints as a durable, lightweight solution that’s engineered for the road ahead.
Contact Us