Universal joints with wing bearings are rapidly becoming a key component in industries requiring robust and efficient torque transfer solutions. The unique design of these U-joints makes them ideal for applications involving high loads and frequent shock impacts. Unlike traditional U-joints, the wing bearing design enables better torque management by transferring power through mechanical allowances, which significantly reduces wear and tear. This feature not only enhances the durability of the entire driveshaft system but also ensures smoother operation, making wing-bearing U-joints highly sought after for demanding applications.
One of the most important advantages of a universal joint with wing bearings is its ability to handle continuous load variations. In systems subjected to fluctuating or unpredictable loads, traditional U-joints may face issues with premature wear or failure due to stress points. However, the wing-bearing design distributes the forces more evenly, ensuring that the torque is transferred with greater stability. This ability to accommodate varying loads ensures that the U-joint performs consistently over a longer lifespan, which is crucial for industries like agriculture, automotive, and heavy machinery, where downtime for repairs can be costly.
The key to the performance of wing-bearing U-joints lies in their innovative mechanical structure. The bearing blocks are equipped with keys that slot perfectly into corresponding grooves on the yokes. This mechanical connection allows for the transfer of torque with high precision, even in extreme conditions. The addition of wing bearings further enhances this effect by providing greater surface contact, thus distributing forces more evenly across the joint. This level of efficiency is particularly beneficial in systems that must operate under high-stress or shock-load conditions, where other types of U-joints might fail prematurely.
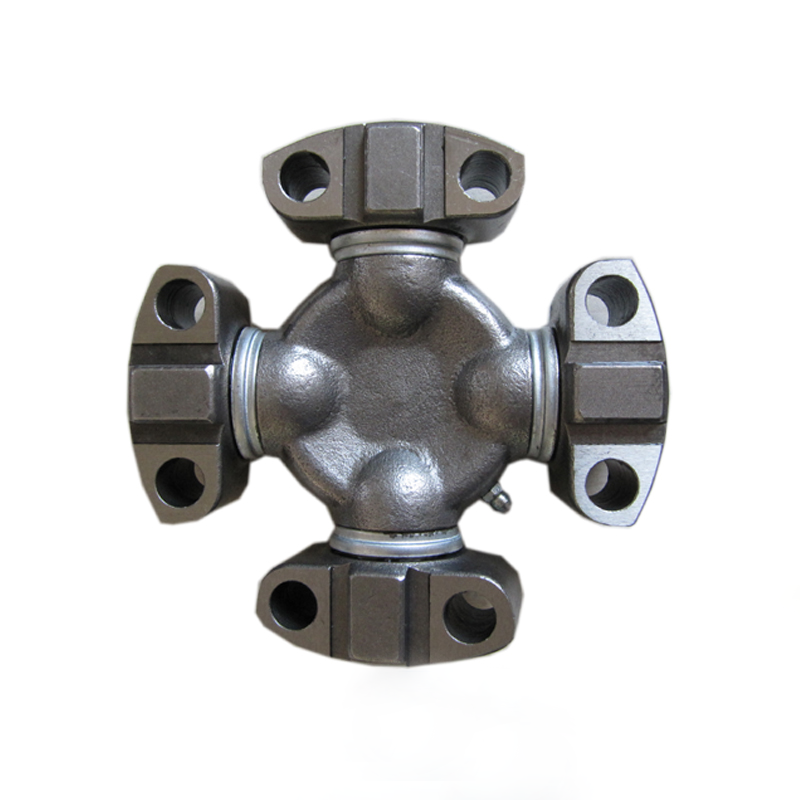
Moreover, wing-bearing universal joints provide enhanced reliability in high-speed applications. The ability to transfer torque smoothly reduces friction, which in turn lowers the risk of overheating or component failure. High-speed vehicles, industrial machinery, and driveshaft systems in rotating equipment all benefit from this design innovation. The reduced wear and more efficient torque transfer ensure that these systems operate smoothly, reducing the need for frequent maintenance and extending the operational life of the equipment.
Another notable advantage of using U-joints with wing bearings is their ability to reduce maintenance costs. Because these joints are specifically designed to withstand continuous shocks and variable loads, they are less prone to failure. The result is fewer replacements, repairs, and overall downtime. For manufacturers, this means greater operational efficiency and cost savings in the long term. Companies that depend on machinery reliability are increasingly turning to universal joints with wing bearings to improve performance while keeping maintenance budgets in check.
When considering the integration of a universal joint with wing bearings into an existing system, manufacturers must take into account the specific requirements of the application. Understanding factors such as the range of expected torque, the environmental conditions, and the type of loads will ensure that the right U-joint is selected. Wing-bearing U-joints offer unparalleled customization options, allowing for a precise fit to meet the specific needs of each customer. Their adaptability makes them a preferred choice for industries with specialized equipment and demanding operational environments.
In conclusion, universal joints with wing bearings offer significant improvements in torque transfer efficiency, durability, and performance. Their ability to manage shock loads and variable stresses makes them an ideal choice for high-performance driveshaft applications. By providing smoother operation and reducing maintenance needs, these U-joints not only optimize system functionality but also lead to long-term cost savings. Whether in heavy machinery, automotive, or industrial applications, wing-bearing U-joints represent the future of efficient and reliable torque transfer technology.
Contact Us